The future of packaging
Hon.-Prof. Dr. Sascha Peters, HAUTE INNOVATION – Future Agency for Material & Technology, Berlin
Guest contribution: Dr. Sascha Peters
The corona pandemic shows once again that plastics in hygiene articles, for food packaging or simply as a protective screen in the checkout area cannot simply be replaced by other materials. Plastics are cost-effective, easy to process and shape, and keep hygienically tight. Sustainable food packaging is still rare.
However, in the form of face masks, disposable gloves or ToGo packaging, they quickly end up in the trash after the work is done, which is currently driving up the volume of waste. Frankfurt’s municipal waste disposal FES recorded a total of 2,608 metric tons of packaging waste in March and April 2020, about 11 percent more than in previous months. The recycling company Der Grüne Punkt was able to detect a 10 percent larger waste mountain from private yellow garbage cans in March 2020. The successes in reducing the amount of plastic that have been achieved in recent years are being reversed in the pandemic.
Ein Umdenken muss her, und das ist nicht erst seit kurzem so. Doch was tun in einem Wirtschaftssystem, das über Jahrzehnte ein lineares Verständnis vom Ressourcenverbrauch hatte und nicht in geschlossenen Kreisläufen dachte. Produkte wurden von Unternehmen und Designern bis zum Zeitpunkt des Verkaufs an den Kunden gedacht und meist nicht darüber hinaus. Es fand eine Entkopplung von der Herstellung der Produkte und ihrer Entsorgung statt, was es jetzt so schwierig macht, das System umzustellen. Die Verantwortung für den notwendigen Wandlungsprozess kann dabei nur auf Basis eines Miteinanders von Kunden, Produktentwicklern und Herstellern sowie den politischen Entscheidern getragen werden, das zeigen die letzten Jahre sehr deutlich. Der stärker werdende Wunsch des Kunden nach einem nachhaltigen Umgang mit unseren Ressourcen und unserer Umwelt wird helfen, das System zu verändern und in Richtung einer funktionierenden Kreislaufwirtschaft zu verändern.
Less is more
When it comes to sustainability, society is divided. While some call for renunciation and proclaim “less is more”, others call for innovations. This split can be observed in almost all major topics: mobility, energy, housing, consumption and nutrition. This summer we were able to observe what “less is more” can mean for industries and countries that are dependent on tourism. The urgent need to move away from plastic-based packaging in order to reduce the volume of waste seems to have been reduced to absurdity, at least in the short term, by the pandemic.
Reuse, refurbish, recycle
The fact that the truth approaches shades of gray in black and white arguments is also known by the many initiatives that have committed themselves to promoting a circular economy. The approaches to the design of the material flows are based on technical and biological cycles. Natural materials and biomass should remain natural, should not be treated or coated industrially and, after the end of the life cycle of a product, should be added to the biological cycle or be available again as natural nutrients. All other materials, especially high-quality materials such as metals, which are produced with high energy input, should circulate in the technical cycle. The adherents of the “less is more” principle can also be found here. Not only should the materials be reused, but resource efficiency should be increased through the repeated use of a product, the processing of components in other areas of use and the recycling of the materials. Great importance is attached to designers in this context. Because by designing a product including the packaging, they lay the foundation for which and, above all, how materials are used and how easily they can be returned to the material flows at the end of the life cycle.
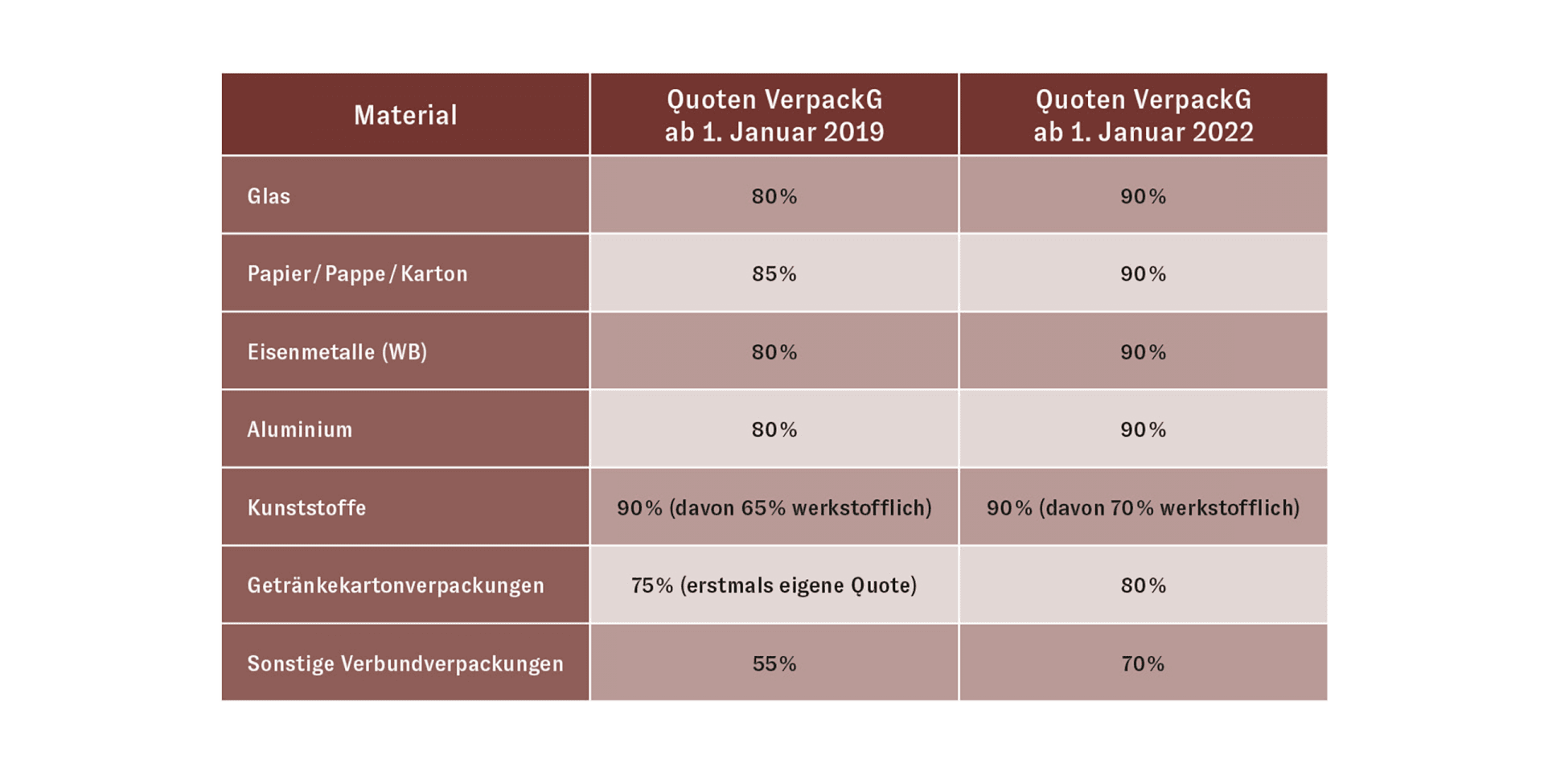
The European Union is planning a recycling rate of at least 65 percent across all types of waste and industries for the year 2035; the aim for landfill is a maximum of ten percent. The differences in the individual countries between actual and target are still clear, but the desire for a functioning circular economy is being formulated more and more clearly. With the Packaging Act, the Federal Republic of Germany is attempting to significantly improve recycling rates in the packaging sector. This is essential, especially for polymer materials and plastics. Because if official bodies assume a current rate of recycling of plastics in packaging of 36-39%, the Wuppertal Institute for Climate, Environment and Energy has a significantly lower rate of 17.3% for 2019 after deducting usable composite materials and exports Plastics calculated. Similar figures have become known from Sweden.
As a consequence, a tightening of the legal requirements is required in order to prescribe the use of recycling material for plastic producers. But if you look at the damage that incorrectly deposited or recycled plastics can cause in nature, in addition to optimizing our recycling system and reducing the packaging volume as a whole, material and packaging innovations for the biological cycle should be in the foreground. Current developments by a large number of designers and companies give hope that there will be many innovations in the field of biodegradable and compostable systems in the future:
A good example of avoiding plastic packaging in the hygiene sector is the “Soapbottle” by Joanna Breitenhuber, which was created as part of a master’s thesis at the UDK Berlin and was awarded the Federal Ecodesign Prize in 2019. As a packaging for liquid washing substances, the Soapbottle itself is made of soap and can be reused as hand soap or processed as detergent after the contents have been used up. Packaging waste is completely avoided because soap is made from natural raw materials and is therefore biodegradable.
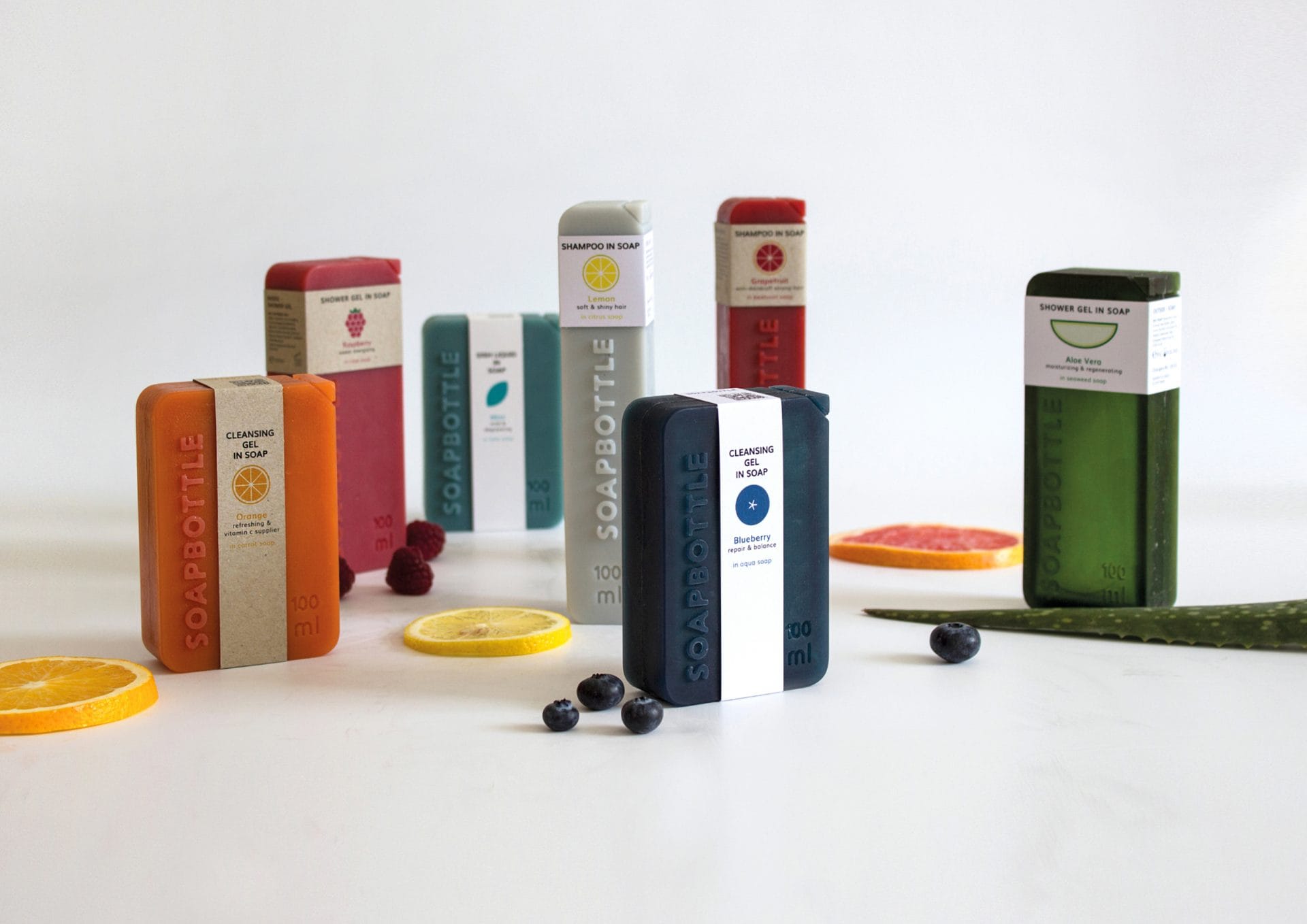
The fact that even agricultural residues are suitable as a resource for packaging systems for the growing online food trade is demonstrated by the Munich-based mechanical engineering company Landpack with its “Landbox” insulated packaging. This consists of straw and can be disposed of in the organic waste garbage can or composted in the garden. According to the manufacturer, the packaging material is produced in a climate-neutral way. This requires only a fraction of the energy needed to produce comparable packaging materials from polystyrene with similarly good insulating properties. The straw used comes from farmers in the area.
The paper industry in particular is one of the innovation drivers in the development of environmentally friendly packaging systems. One example is the development of “Compostella,” a high-purity specialty paper made from unbleached wood cellulose, water and sugar that can replace conventional aluminum foil, cling film and siliconized baking paper. Because thanks to the mechanical treatment of supercalendering, it is greaseproof, heat-resistant and suitable for direct contact with food. In the production process, the material is passed over hot steel rolls and pressed extremely tightly as well as highly compacted. It does not contain any chemical additives and is neither coated, painted nor impregnated. The wood used comes from Scandinavian thinning wood, which is obtained during forest maintenance.
In recent years, a number of companies have been trying to develop an environmentally friendly alternative to PET bottles based on paper. These should have sufficient impermeability for the transport of liquids and should be able to degrade in nature after use if disposed of improperly. The “Green Fiber Bottle” is a development from Denmark and is said to be 100% bio-based and fully recyclable. In late 2019, a research prototype was unveiled that was made from sustainably sourced wood fiber and included an inner barrier layer made from a bio-based PEF polymer film barrier that has no negative environmental impact. Originally, when development started, it was still assumed that a thin glass coating would be used inside the packaging.
Developments by designers who are currently not only innovators but also as entrepreneurs and producers on the market show that resources from the sea are particularly suitable for the development of biodegradable materials for packaging want to establish.
Vietnamese designer Uyen Tran, for example, combines the biopolymer chitin with coffee grounds to create a sheet material called Tômtex. Chitin is not only the main component of the exoskeleton of insects, but it is also found in mussel shells and the shells of shrimps and other marine crustaceans. The word “Tôm” means “shrimp” in the Vietnamese language, thus giving an indication of the most important component of the biodegradable sheet material that can be used in packaging systems.
With MarinaTex, designer Lucy Hughes has developed a compostable material based on waste from the fishing industry such as fish scales and red algae as an alternative to single-use plastic films in her final thesis at the University of Sussex. Most biodegradable bioplastics used in packaging today can only be composted at high temperature and humidity in industrial facilities. In contrast, MarinaTex can also be returned to nature in the garden or in the home at temperatures between 7 and 26 °C in four to six weeks. In 2019, the innovation won the James Dyson Award.
The fact that home-compostable disposable packaging based on resources from the sea has already arrived on the market is demonstrated by the British start-up Notpla with its Ooho solutions. The packaging for beverages and spicy sauces is based on algae extracts and vegetable ingredients and is biodegradable in a few weeks or can even be consumed. The manufacturing process is based on the possibility of encapsulating liquids by “spherification,” which originated in molecular cuisine. In this process, the alginate contained in algae reacts with calcium ions as a thickening and gelling agent and cross-links to form a three-dimensional sponge mesh. Notpla has now developed the technology to the point where Ooho could eliminate the waste problem from large events by replacing plastic cups and bottles. For example, the company has already provided 35,000 Oohos to runners in the 2019 London Marathon.
It looks like innovations in the biological cycle can make a significant contribution to reducing the amount of waste in the packaging sector and to designing closed material cycles. The future will show how many of these exciting innovations will establish themselves on the market and how they will be accepted by the food companies.